Understanding how LIBS technology delivers greater yields of higher quality aluminum scrap in recycling is a key in boosting the bottom line. Austin AI and Ocean Optics partnered with a large British recycler to do just that.
Aluminum is the most abundant and environmentally friendly metal on earth. Quite often referred to as the “green” metal, aluminum is sustainable, and is capable of being recycled and reused without loss of its inherent properties. Aluminum recycling is one of the most efficient forms of recycling, using up to 95 percent less energy than creating aluminum materials from virgin materials (primary production).
Globally, aluminum demand is up while primary production is down, with recycled aluminum expected to help fill the gap. Primary aluminum producers are creating new products that have substantial amounts of recycled aluminum driven in part by:
- the high energy costs to create primary aluminum,
- consumer demand for more environmentally friendly products, and
- corporate sustainability goals.
In aluminum recycling, scrap aluminum is sorted into different grades, lights and heavies. Once preliminary sorting is done, the lights can be sold as mixed-grade to an aluminum producer to create new alloys for production or re-processing. However, the more precise the separation into individual grades, the higher the value of the scrap aluminum. A steady stream of highly sorted aluminum scrap means fewer melt adjustments with primary aluminum and a far “greener” product.
This article details the justification and implementation of a fast, effective sorting system developed by Austin AI and utilizing Ocean Optics LIBS sensor, in conjunction with H Ripley and Co, Ltd., one of the UK’s largest scrap metal recyclers.
The Problem
Fast, cost-effective aluminum sorting has long been a desire for scrap recyclers. H Ripley and Co, based in Hailsham, UK, is a fifth-generation, family-owned scrap yard in business for over 100 years. Like many yards, Ripley has dealt in ferrous and non-ferrous scrap since their inception. However, unlike most other yards, they also have been shredding aluminum for over 30 years.
Jason Ripley, commercial director with H Ripley and Co, realized long ago that there was significant value that could be extracted from aluminum if the right sorting tools existed. His company was selling mixed aluminum that contained multiple premium grades, as a fast, cost-effective sorting tool was not available to separate the grades and alloys, and hand sorting was not an option. “The concept and need have been there all along,” said Ripley. “There just was not the right technology to sort aluminum quickly and effectively.” The significant uptick in aluminum demand further drove this need over the past decade.
H Ripley and Co, like other scrap recyclers, is a user of handheld XRF (X-ray fluorescence) and is aware of online X-ray solutions. While a good option for heavy metal sorting, XRF does not lend itself well to sorting aluminum. Jason Ripley was introduced to an Austin, Texas-based company named Austin AI by one of his customers, a large UK extrusion ingot and sheet ingot producer. This company had success with Austin AI’s solution and urged Ripley to investigate.
Sensor Sorting Technology
Rick Comtois, CEO for Austin AI, is a veteran of elemental analysis and has focused on online sensor sorting technology for over 20 years. Having previously implemented numerous units based on both Nuclear Magnetic Resonance (NMR) and XRF technology, Comtois began to shift his focus to Laser Induced Breakdown Spectroscopy (LIBS) in 2014. Comtois says that LIBS technology offers unparalleled light element technology that is not feasible with other methods.
Austin AI’s interest in light element sorting solutions led to a relationship with Hydro Aluminum (hydro.com) in which Austin AI built a sorting system for culling Aluminum 6063 from construction and demolition (C+D) material. The result of this process for Hydro Aluminum and any secondary smelter was melt-ready “green material,” allowing them a much-desired lower carbon footprint.
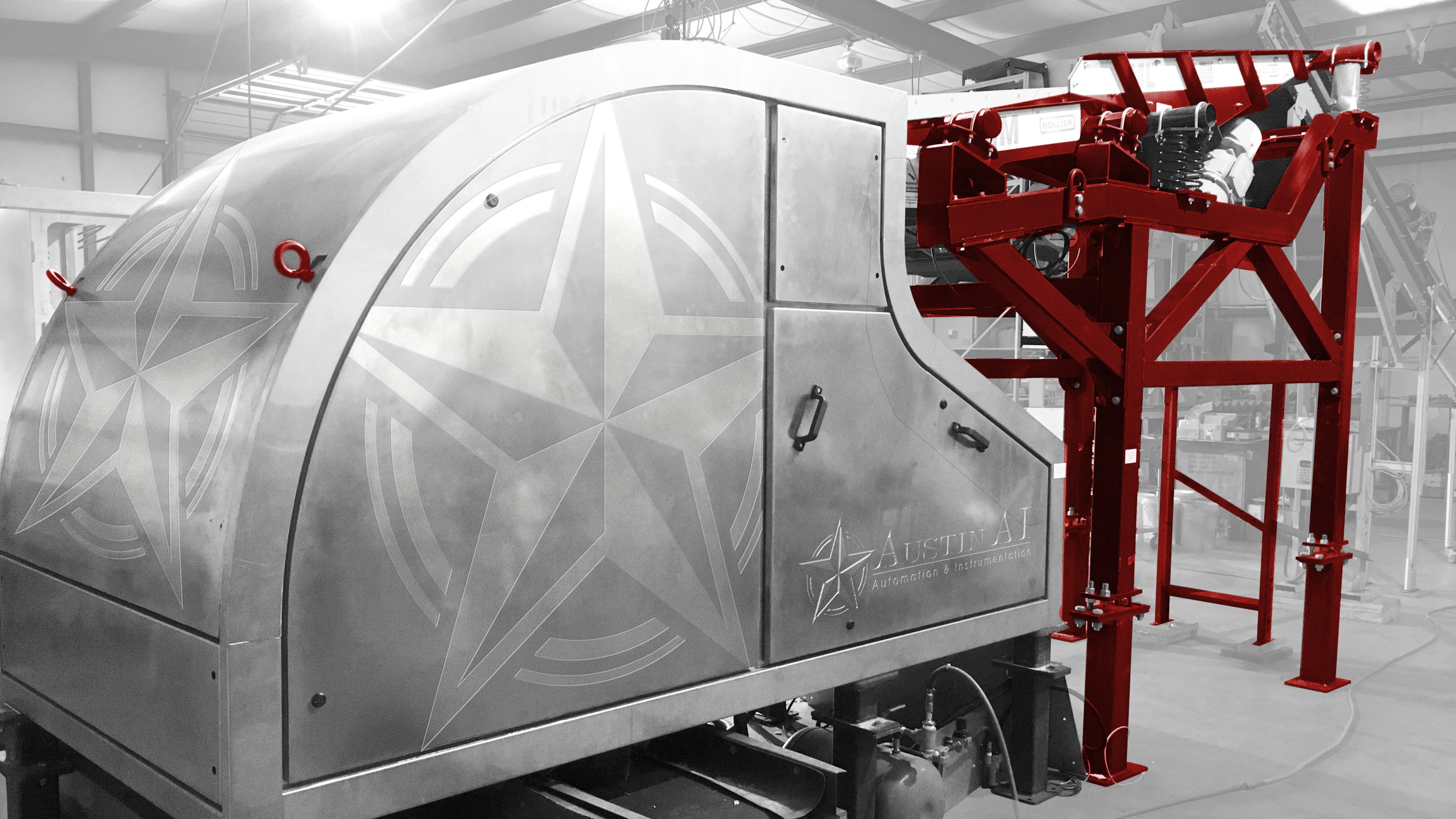
Figure 1. Austin AI’s scrap aluminum sorting system integrates Ocean Optics LIBS-based SpeedSorter for more precise sorting of the most desirable aluminum grades.
Austin AI’s LIBS sorting system (Figure 1) offers the following advantages:
- Reliable, robust modular design with minimal moving parts
- Flexible setup with either 1 or 6 sorting lanes; a 6-lane design allows for a LIBS module to be internally replaced to maintain uptime
- Chute design where sample drops in front of the LIBS laser, which eliminates the need to adjust focal distance per sample
- Feasibility for clean production scrap as well as post-consumer scrap with no pre-ablation needed
- Lowest fully loaded cost-per-weight ratio in the world
- Compatible with Ocean Optics SpeedSorter LIBS sensor
Online sorting provides significant advantages over manual sorting, including increased speed, accuracy, consistency, and efficiency. It also reduces labor costs, increases safety, and provides valuable data for optimizing aluminum sorting.
Rick Comtois explained the return on investment with online sorting: “I estimate the fully loaded cost — which includes the initial system cost, the operation cost, the labor cost and more — to be a few cents per kilogram when running our sorter at 4-5 tons/hour. This cost is outweighed by the premium pricing gained per truckload for melt-ready scrap.”
LIBS and the SpeedSorter
Laser induced breakdown spectroscopy (LIBS) is a form of atomic emission spectroscopy using an energetic laser pulse highly focused at the sample surface to convert a small mass of a sample to plasma, causing the atoms and ions to emit their characteristic emission lines. For many, LIBS is recognized as optical emission spectroscopy (OES) that uses a laser instead of an arc or spark source. LIBS has been used for almost five decades in laboratory and research environments.
Recent technological advancements have made the design of online LIBS sensors, like the SpeedSorter (Figure 2) from Ocean Optics, possible and available for use in industrial applications. This development rapidly expanded the use of LIBS, especially into field operations such as aluminum sorting and analysis.
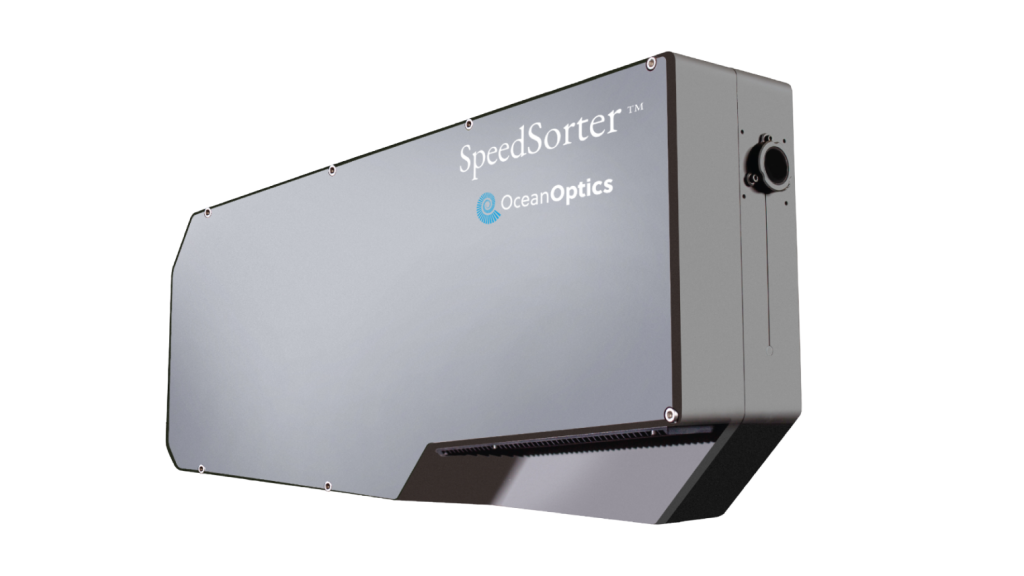
Figure 2. SpeedSorter utilizes LIBS technology to rapidly sort nonferrous scrap metals in industrial environments.
Since LIBS is better suited than handheld XRF for analysis of light elements such as lithium (Li), aluminum (Al), magnesium (Mg), and beryllium (Be), it is quickly gaining industry acceptance as a method of choice for sorting specific alloys from aluminum scrap.
Ocean Optics SpeedSorter is an industrial, high-throughput sensing system designed for in-line, nonferrous scrap sorting in difficult environments. Based on LIBS, the SpeedSorter quickly determines the chemical composition of each aluminum scrap object and communicates the result to Austin AI’s sorting system. With the SpeedSorter, separation of wrought from cast aluminum, aluminum from magnesium, and alloy class separation like 6XXX from mixed aluminum scrap are easily accomplished.
The SpeedSorter can be customized to the customer’s exact needs with consideration of conveyor capabilities, input material and size, and desired output and diversion control.
“Ocean Optics created the SpeedSorter, which has enabled LIBS metal sorting to be commercially viable,” explained Lu Luo, Vice President at Ocean Optics. “It has overcome past LIBS sensor issues with capabilities to sort several tons per hour, obtain high purity with post-consumer scrap and even sort exact alloys from Twitch or Zorba [types of aluminum scrap].”
H Ripley ’s Online LIBS Sorting Technology
H Ripley began to implement Austin AI’s Sorting System late in 2020. The project goal was to implement a solution for retrieving a steady stream of 6063 aluminum alloy from mixed aluminum scrap. Working closely with both Austin AI and Ocean Optics, Ripley integrated the LIBS sorting system for the sorting of shredded, clean, dry material, post-magnetic and eddy current separation.
Prior to the implementation, Ripley primarily processed and sold mixed aluminum to markets in Asia. Post-implementation of the sorting system, Ripley is segregating and selling the valuable portion to a large UK extrusion ingot and sheet ingot producer.
Ripley’s client has been pleased with the 6063 aluminum alloy received, which is within their specified tolerance and standard (Figure 3). Copper and zinc removal is key as the extrusion producer was looking for material that is below the 0.1% max allowable amount of each. Lower, in this case, is always better.
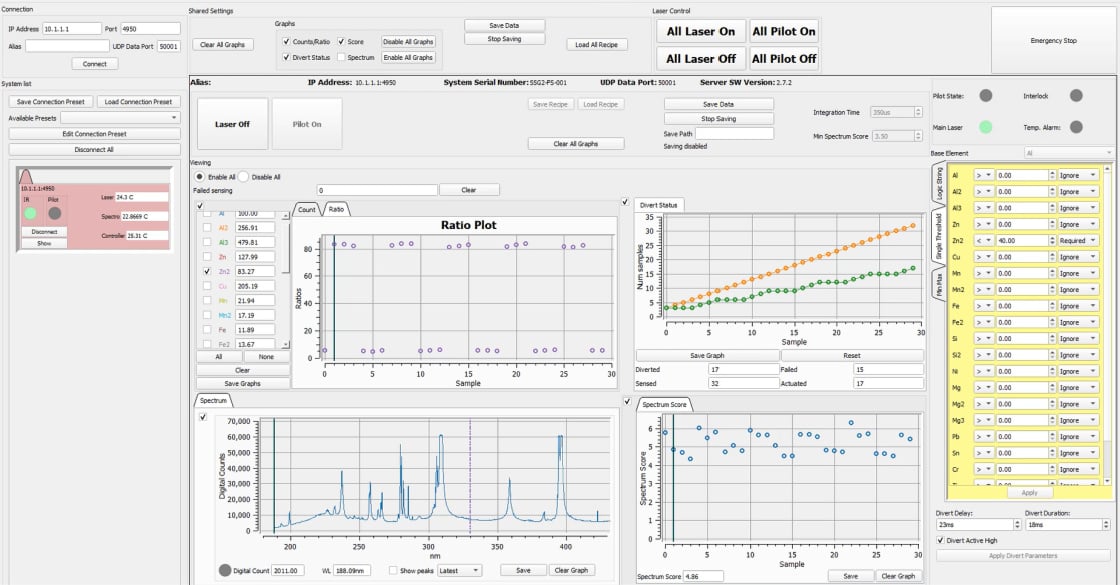
Figure 3. A sophisticated yet simple to understand user interface is an important feature of the SpeedSorter, with minimal operator training necessary to start sorting.
The following is the Alloy EN AW‐6063 (AlMg0.7Si) specification that Ripley sought to achieve:
Element | Specifications |
Si | 0.2-0.6% |
Fe | 0.35% (max) |
Cu | 0.10% (max) |
Zn | 0.10% (max) |
Mg | 0.45-0.9% |
Cr | 0.10% (max) |
Mn | 0.10% (max) |
Others | 0.05% each (max 0.15%) |
The UK extrusion ingot and sheet ingot producer has been extremely satisfied with their material. Ripley’s LIBS sorter has provided them with a “worry-free,” low carbon footprint stream of Low Cu and Zn 6063 material.
Although some unforeseen issues meant the LIBS Sorting System was configured to its final operation mode months later than expected, Jason Ripley said all parties worked with urgency: “Austin AI, Ocean Optics and Ripley had a common goal of getting this project over the finish line, so we had no doubt that the unit would be up and running and working effectively for us as soon as it was possible.”
Through the first several months of operation, Ripley has been running 3-4 tons of material per hour through the sorting system. As noted by Rick Comtois and Jason Ripley, material should be dry as material flows (moves through the system) better when it is not wet. Material size can vary but 5-6 inches is considered mid-range and best for higher throughput. Additional screening within the process will further assist with the purity of the material obtained.
Path Forward
Jason Ripley is proud to see the LIBS Sorting System implemented at his facility. He knew for decades that the need was there, and that the technology would eventually be available to make it happen.
Ripley and Co. is finding that the industry is not aware of LIBS or that this type of sensor technology exists. This has made expanding Ripley’s customer base more challenging than initially thought. Jason Ripley has mentioned going as far as to sponsor a trial load of LIBS segregated material for new clients for them to fully grasp the capability the technology has.
Austin AI’s Sorting System with integrated SpeedSorter does offer clients like Ripley the ability to change sorting programs to allow for segregating whatever alloy and tolerance are needed. This will allow Ripley to add customers more easily with specific application requirements.
Ongoing installation of the LIBS Sorting System at other yards that process large amounts of nonferrous metals will help with adoption as will further use of handheld LIBS-based systems, which are growing in popularity for light element analysis within the scrap industry.
Austin AI and Ocean Optics are pleased to offer the aluminum industry a rapid and effective solution for recovering melt-ready nonferrous scrap. The LIBS Sorting System facilitates efficient recycling, conserves resources, reduces energy consumption and emissions, and promotes the transition to a circular economy, which collectively contribute to a greener environment and meeting sustainability goals.